Customer-centric Data-driven Evidence-based Decision-making
In a world swamped with expectations, opinions and hearsay, let evidence be your compass and data be your North Star. Informed decisions, rooted in facts rather than opinions and gossip, pave the way for understanding, progress and team effort in a win-win journey.
"Six Sigma is more than just a quality system – it's a way of thinking that empowers people to make decisions based on data, not opinions." – Dr Mikel J. Harry, one of the co-creators of Six Sigma
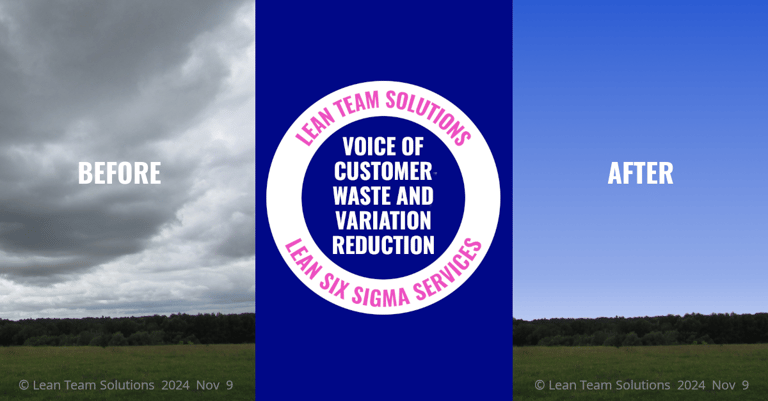
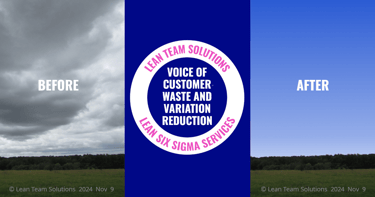
Click to view 4-minute video introduction on what is Six Sigma and why it is needed - from our Founder Director
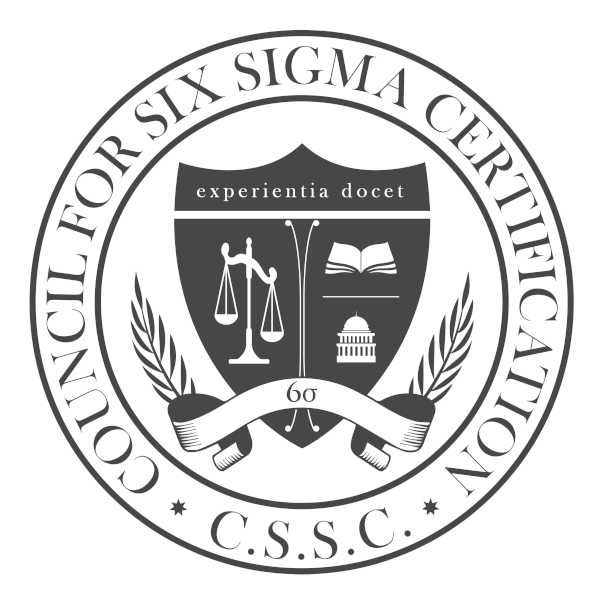
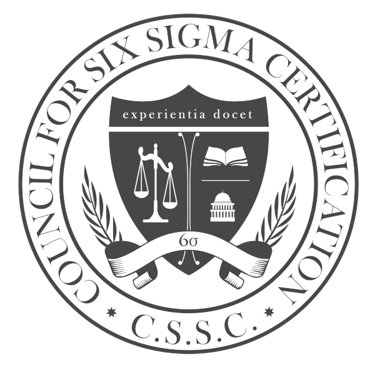
Lean Team Solutions Ltd. is accredited as a Six Sigma Training and Certification Provider by the Council for Six Sigma Certification (C.S.S.C.) .
What we are good at?
We provide the springboard in one’s journey with Lean Six Sigma to reduce waste and variation, improve efficacy and efficiency in process and quality that will elevate customer satisfaction.
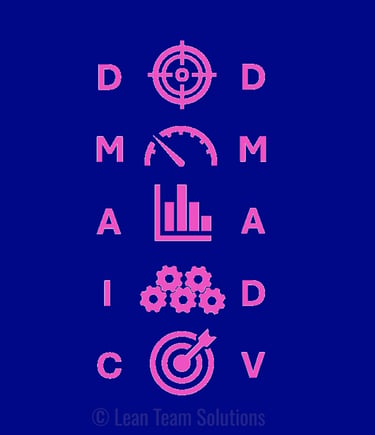
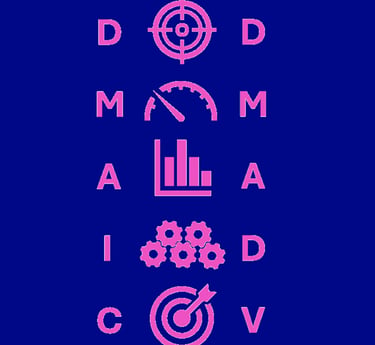
Tried and tested methodology
to improve business, quality and process problems
Today's business environment is increasingly dependent on data and information. Business crisis meetings can get overly emotionally driven, stressful and not conducive to making appropriate decisions. Lean Six Sigma helps staff to measure, analyse and understand the data that helps to find the root cause of the problems.

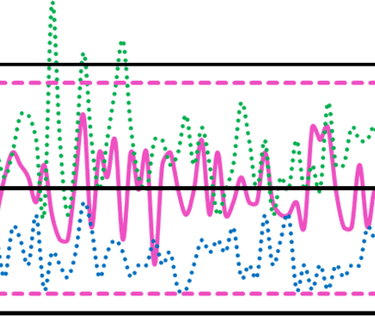
Knowledge & Skills training staff to focus on Data, not Opinions or Gossip
Staff may find it confusing, challenging and demotivated by the amount of information and reports that do not reflect reality. Staff can be trained to interpret, analyse and understand data, thereby enabled with confidence to take improvement actions.
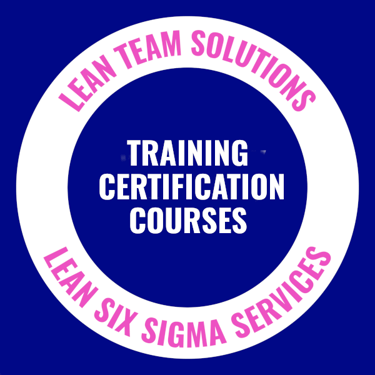
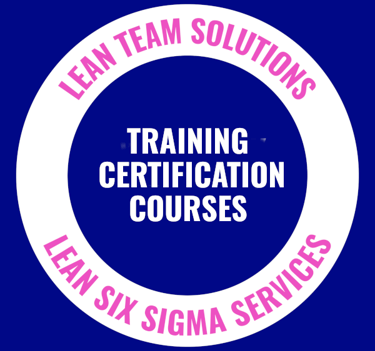
Data measurement, analysis & improvement
It can be daunting to face up to challenge existing Products, Services and Processes. It may require courage to say, "we do not know how, we are not good enough, but we have to learn and make improvement". Invest in skills development with tried and tested methodology to acquire the necessary knowledge, skills and confidence to challenge the status quo.
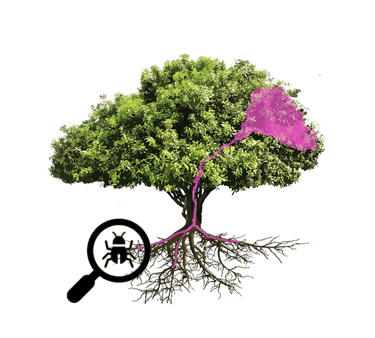
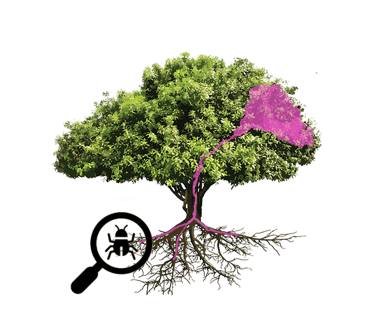
Visualisation of results
Visualisation of data in a pictorial format facilitates easy understanding and discussion thereby enabling focus on root cause of problems. It beats reading intensive text reports which often run into hundreds of pages.
Let us help you
Our approach
1
Business Challenge Review
Define and understand your business goal and performance - what timeline you're at, established or new start-up, plain sailing or in crisis. What challenges you are facing, Voice of Customer needs for your Products, Services, Processes, Staff abilities and skills. Are present skills and abilities of staff adequate or may need up-skilling for the challenges?
2
Review relevant data from measures
Must-have, accurate and measured data with actual and relevant information about and accountable within your processes.
3
Data Analysis
Analyse data from your processes, visualise and understand the wastage and variation. Root Cause Analysis to determine the underlying reasons for non-conformance and failure.
4
Pilot trials to verify and validate changes
Trial proposed changes or new product/process, get evidence to verify and validate improvements in a controlled pilot run.
5
Business Implementation
Successful confirmation of Pilot run leads to upgrade or for new product launch. Implementation often happens in phases paired with vigorous testing. Benefits review to confirm achieving defined goals and objectives, benefits achieved, or new product launch.
Our approach to improve business, process and quality prescribes a logical structure with sequence of steps. This avoids emotional and crisis driven banter which usually gathers reactionary individual opinions and ideas of the moment.
Lean Six Sigma provides the technical data-driven framework for business, quality and process improvement. Bloom’s Taxonomy spells out the attributes for effective learning, acquiring knowledge and practise with new skills in the work environment (crisis meeting!).
How will you potentially benefit?
“An investment in knowledge pays the best interest.” – Benjamin Franklin
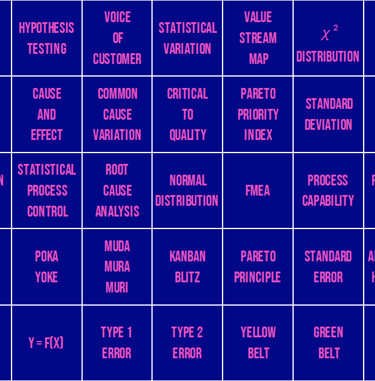
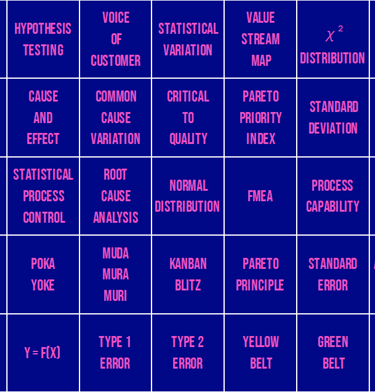
Problem solving skills
Organisational Requirement
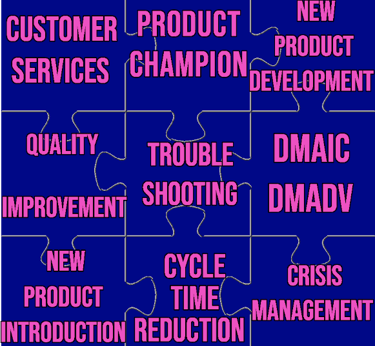
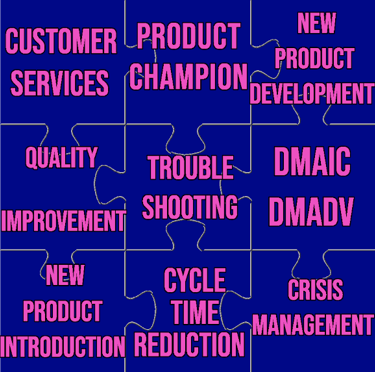
Leadership opportunities
Career advancement opportunities
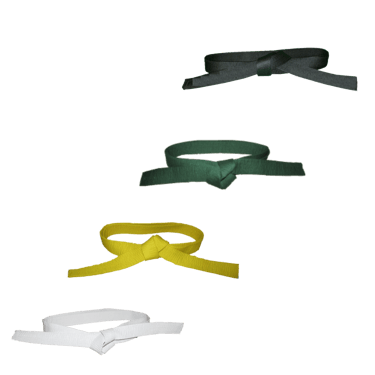
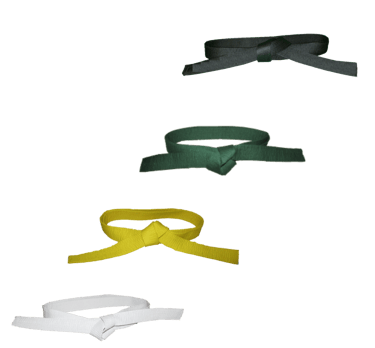
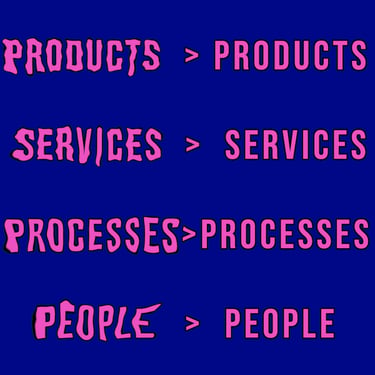
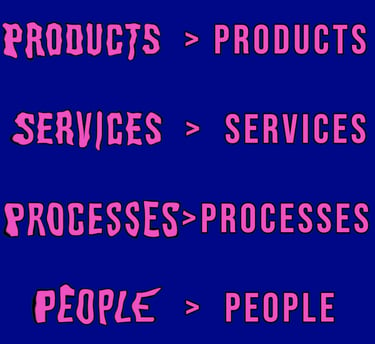
Improve organisation performance
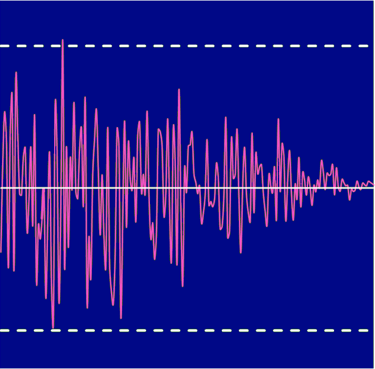
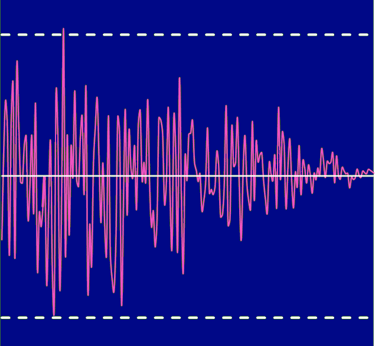
Visualise quality improvement
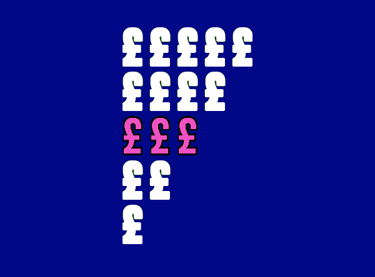
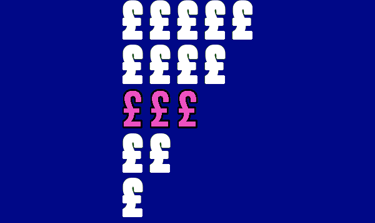
Affordable value training and certification
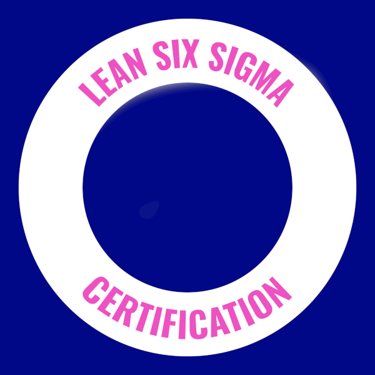
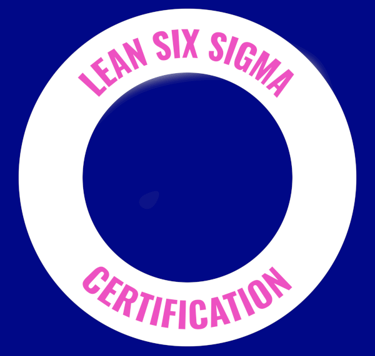
Job security with six sigma skills
Please note: Our training services strive to impart the knowledge and skills of Lean Six Sigma methodology, tools and techniques to our learners.
"Give a man a fish, he feeds for a day. Teach a man how to fish, he feeds for life" - various sources
The proficiency of learners is dependent in consistent execution after completing formal training and certification course.
The degree of benefit achievable for each learner is proportional to effort, diligence and resolve in effective application to solve practical problems in the work environment.
"Success is not given. It is earned!"
Process and Quality Improvement achieved with Lean Six Sigma
Defects Reduction Motorola Manufacturing, ISO 9000 certification, CE compliance marking, New Product Development & Introduction, Design for Manufacturing/Test, Instrumentation, Personal Computers Manufacture and Test, Mental Health Services, Church Services "Who Cares?"
Companies known to have implemented Lean Six Sigma:
General Electric (GE)
Motorola
Toyota
Bank of America
Caterpillar
Honeywell
3M
Amazon
Ford Motor Company
Xerox
Lockheed Martin
Dell
Johnson & Johnson
Citigroup
Verizon
HSBC
Whirlpool
Northrop Grumman
DuPont
Merck
What organisations have implemented Lean Six Sigma?
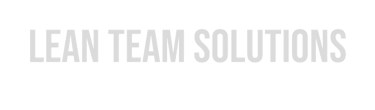
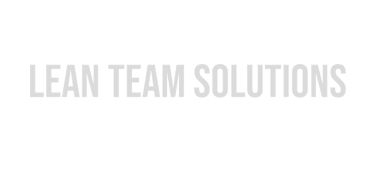
Location
Registered Office: Lean Team Solutions Ltd., c/o Goringe Accountants, Waterside, 1650 Arlington Business Park, Theale, Reading RG7 4SA
Hours
Mon - Fri 9:00-17:00
Sat - Sun Closed
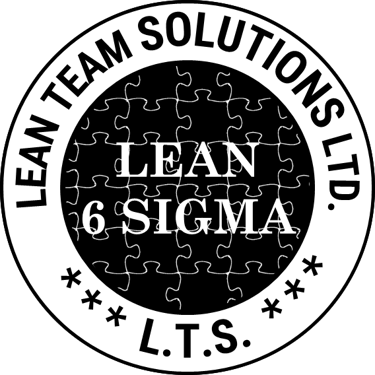
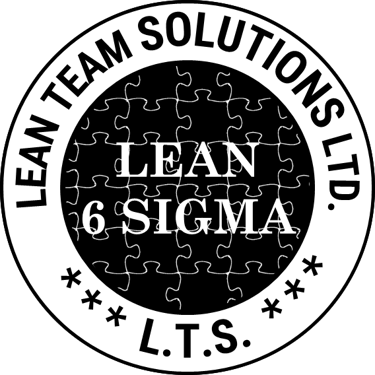